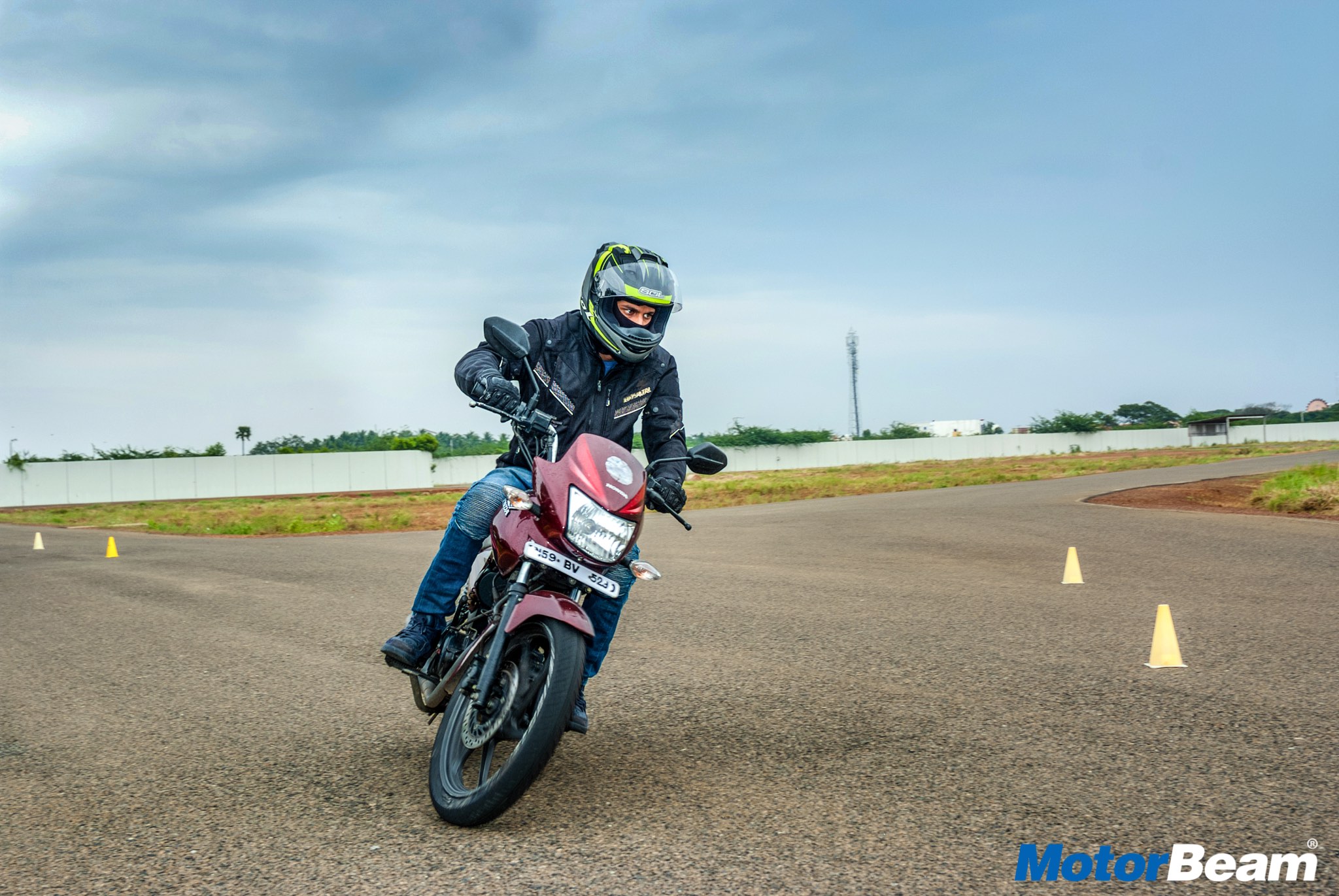
TVS Srichakra Tyres
TVS tyres is the company that makes EuroGrip tyres while also making Michelins
Towards the end of November, we were invited to the beautiful, historic and Holy city of Madurai by TVS Tyres to test their new range of tyre. Now I’ll give you a quick rundown on TVS tyres if you’re unaware of them and the impact they’ve had on the tyre industry in India. TVS Tyres came into existence in 1982 and ever since then have been making tyres for the 2 and 4-wheeler market. TVS Srichakra supplies their tyres to some major automotive companies like Bajaj Auto, TVS Motor, Yamaha, Hero and Honda. They’ve won multiple awards like the TPM Excellence Award in the year 2003, the TPM Consistency Award in the year 2005 and the Energy Conservation Award from the Government of India. These are some of the achievements they’ve had in the history of the company. They globally export their tyres to South East Asia, South America, Europe, USA, and Africa. As our journey began in Madhurai, we were first taken to their factory where they make all these tyres. The factory is huge and we were given a warm welcome before proceeding for lunch, after which we were given a factory tour.
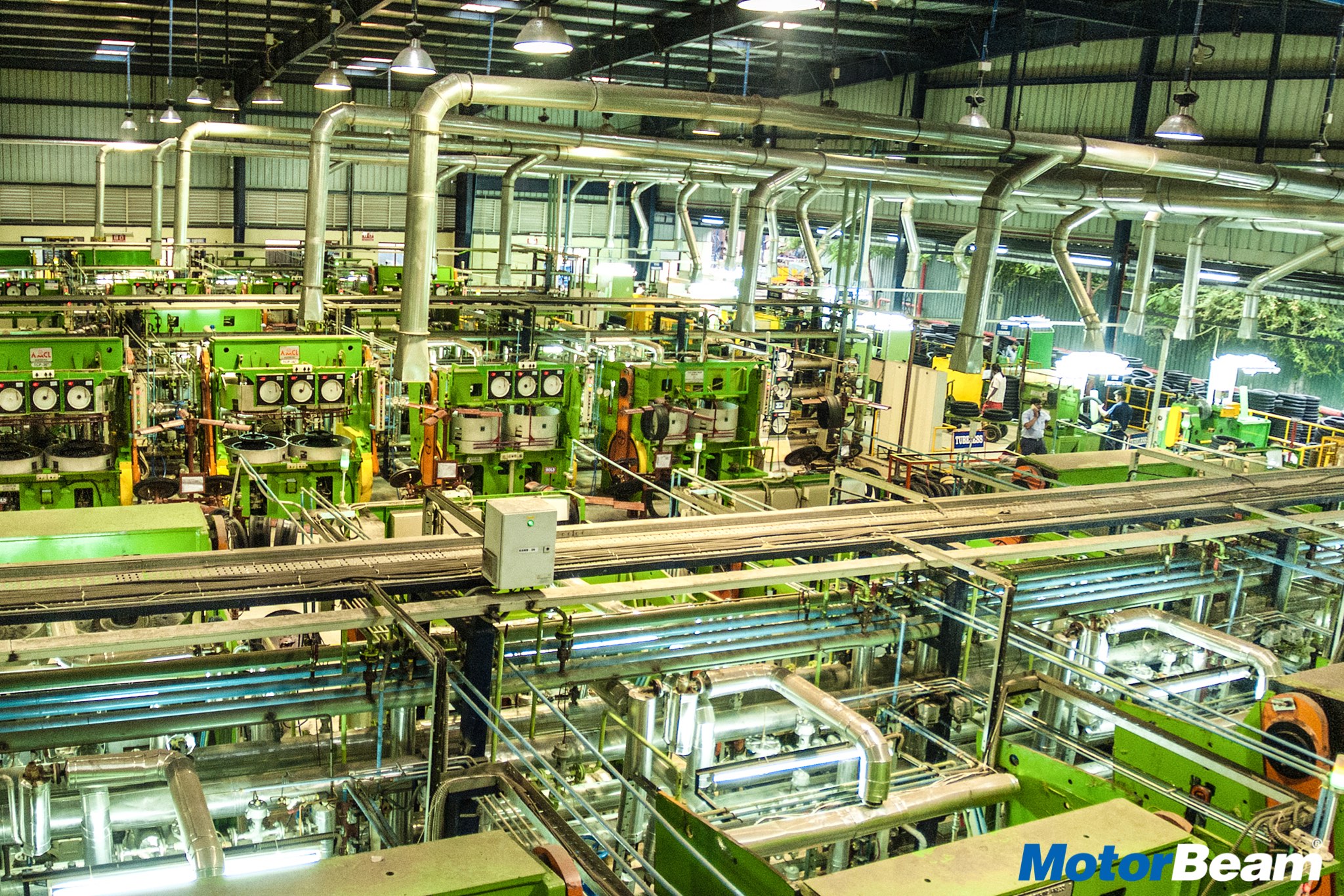
I must say TVS Tyres really likes to focus on quality. Everywhere you looked, everything just seemed so well organized and work was being carried out in the most efficient way. We were shown the entire tyre making process. A tyre can be a complex assembly of many elements, implementing a variety of raw materials. The composition of the rubber compounds varies within a single tyre. Each compound is carefully developed to meet the manufacturer’s requirements in terms of grip, resistance and flexibility. Manufacturing of a tyre is performed on a drum, a rotating cylinder which has a central flexible section that can be inflated. First, a sheet of airtight synthetic rubber is added to the drum which now works as a replacement for the inner tube that we’re used to seeing in older tyres. In the second stage, a ply made of textile cords, blended with rubber is then added. This network of cables helps to reinforce and radiate around the tyre, it is called the radial carcass. It’s braced against strips of profiled rubber and high resistance metal cable hoops, these are the lead wires, they hold the tyre on the rim. The casing ply is then folded over the beads to anchor it and a few other elements are added to it, like sidewalls made of flexible resistant rubber work to protect the tyre from lateral damage.
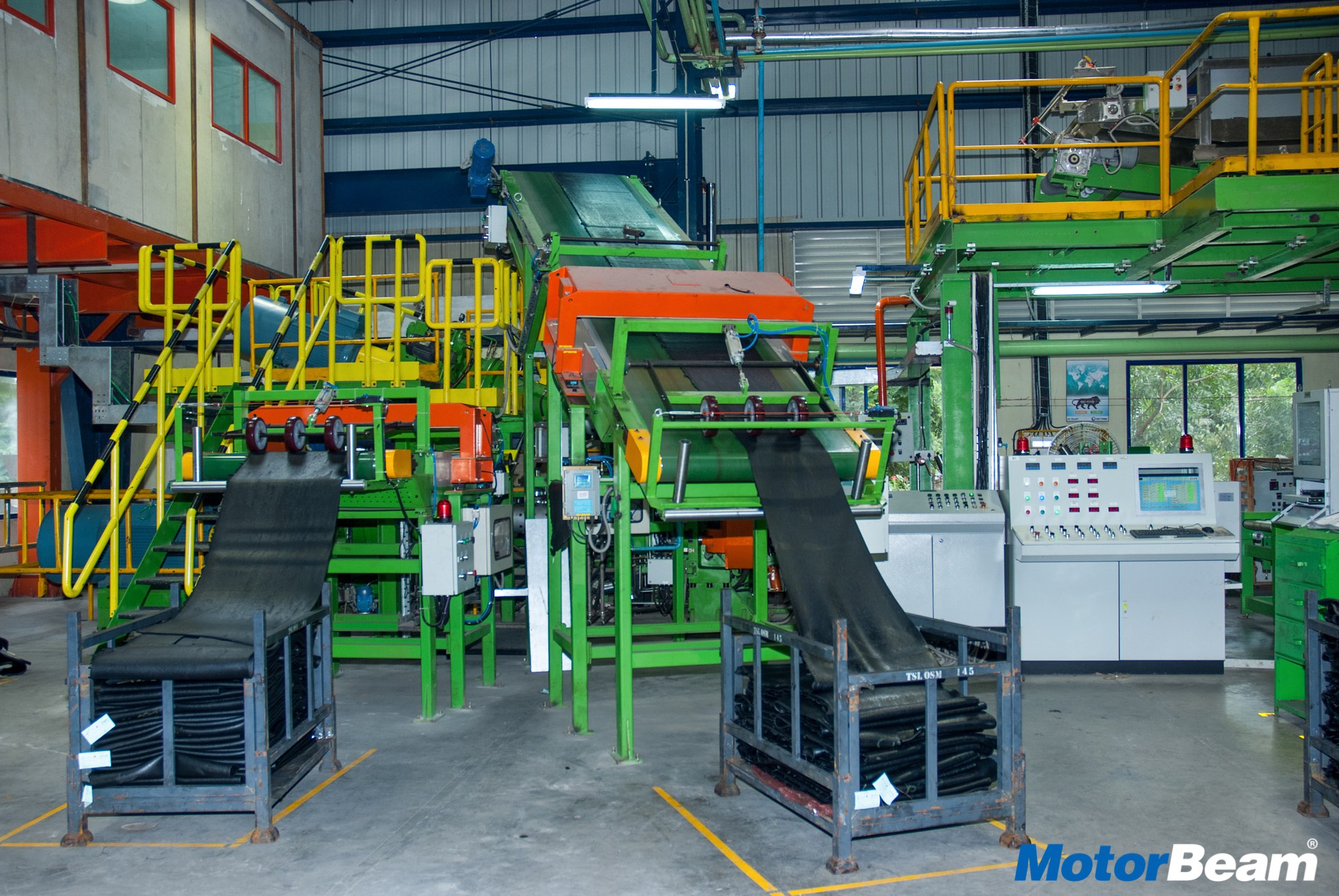
The tyre is then shaped by inflating the central section of the drum, two plies are then applied to what’s known as the crown of the tyre, they are reinforced with metal wires, arranged completely and with the casing ply, form a network to limit the deformations of the tyre. Finally, the tread is fitted, which will be a part of the tyre in contact with the ground. The tyre is then installed in the curing mode, in the center of which a bladder filled with pressurized hot water pushes the still malleable material to the base of the pattern engraved in the mode. The heat of the water and steam surrounding the mold will cause curing to begin, the rise in temperature then causes vulcanization of the rubber.
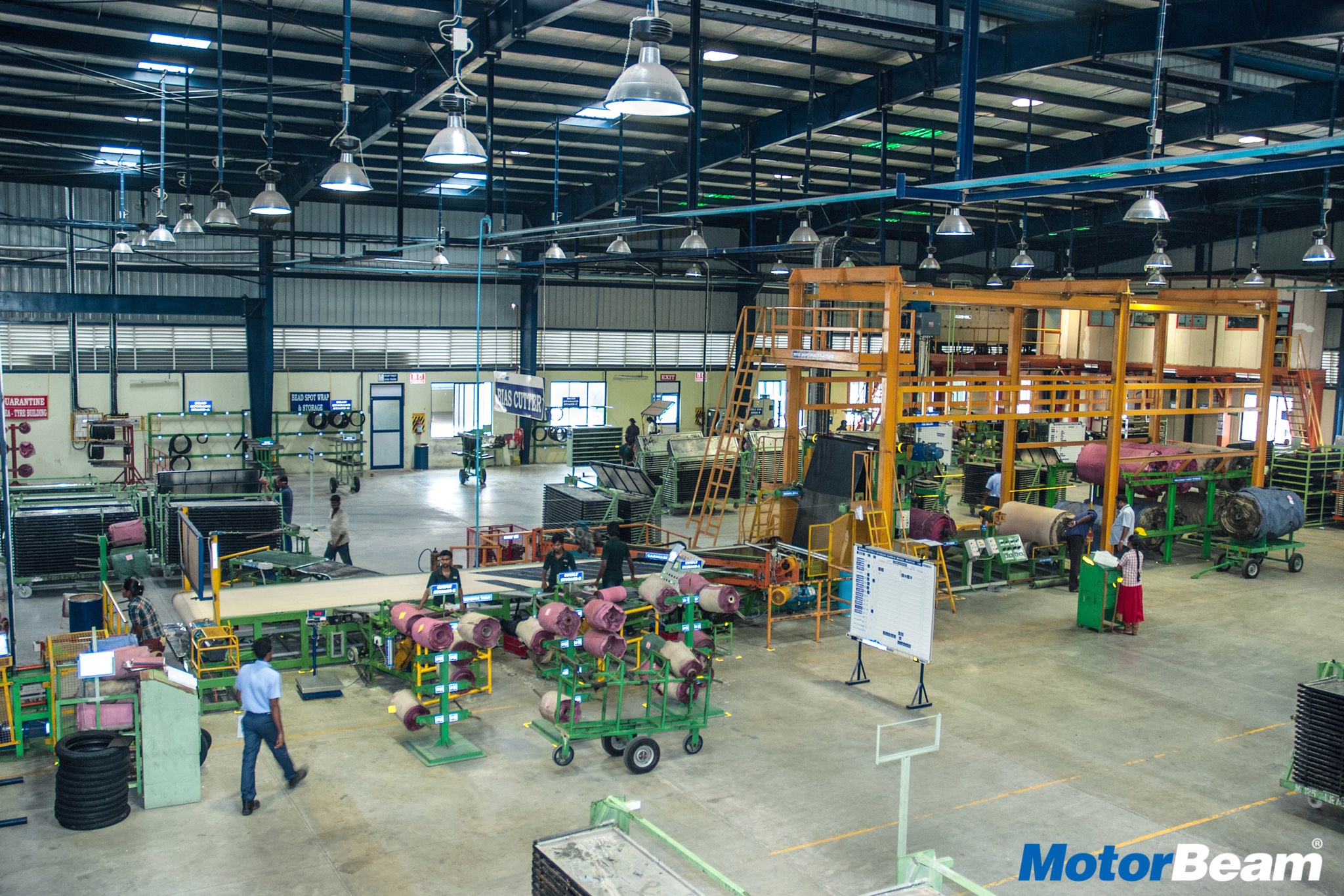
The sulfur incorporated into the rubber components forms bonds between the polymer chains, at this point, rubber changes from a plastic state to an elastic state. When removed from the mold, the tyre has acquired its form and properties, and is ready for road use and testing. Once we were done with our factory tour, we were escorted to the conference room where we were shown TVS Group’s future plans and goals and how they came to be where they are, which was pretty cool to see how globally involving and empowering an Indian manufacturer could be.
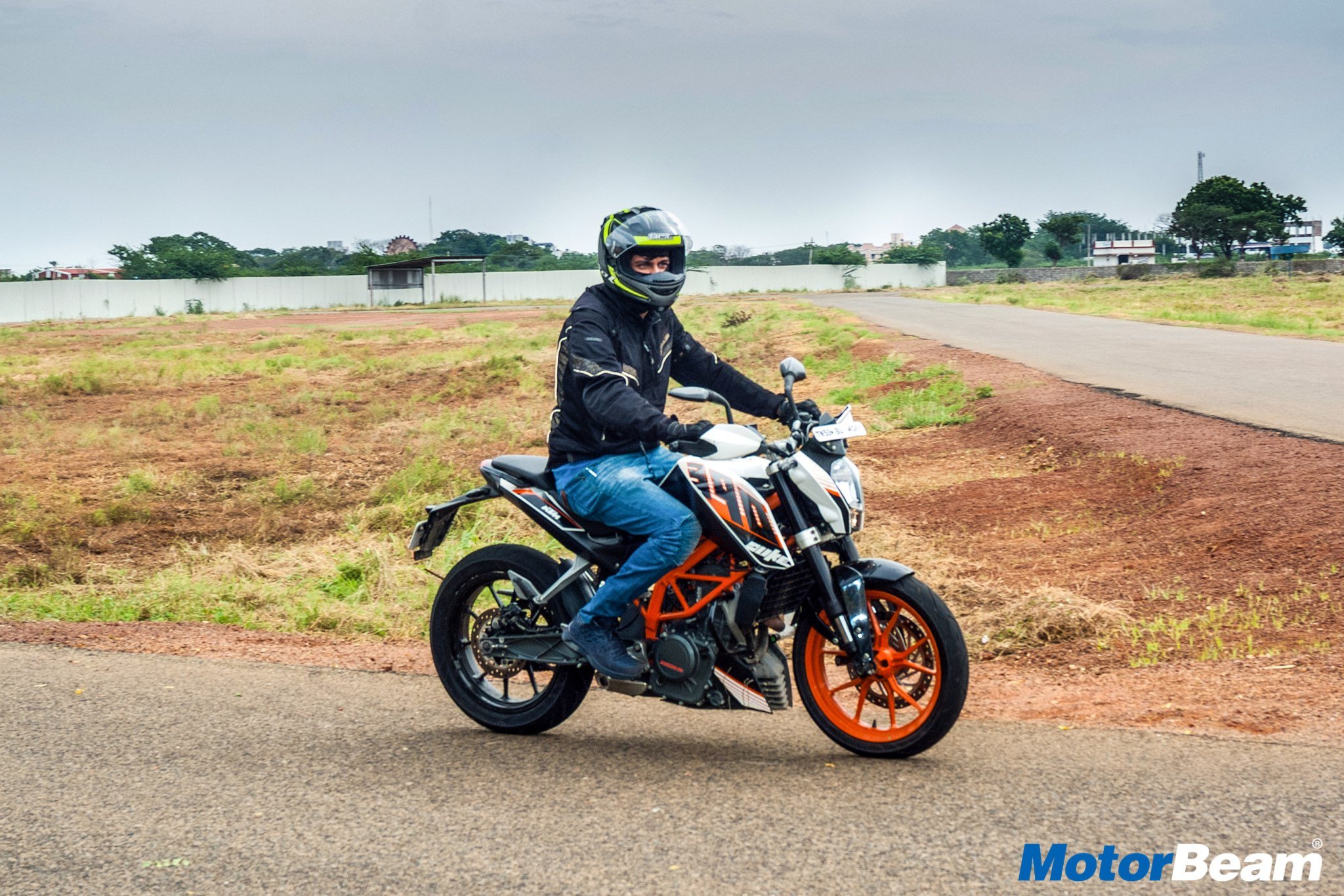
TVS Srichakra’s test track in Madurai is where they test and develop all their tyres
The next day we were scheduled to meet Mr. Hide Okamoto, who’s the person responsible for testing all of the tyres the company has developed in the past years. It was great meeting him, he had so much knowledge to share with his 30 years of professional riding experience. That’s right, 30 years of professional riding, racing, and testing experience. He taught us how to assess and understand the characteristics of a tyre and how each manufacturer individually tailored their machines to suit the handling which they prefer. He told us that no motorcycle handles bad, it’s just that each manufacturer has a preference on how they’d like their motorcycles to handle and ride.
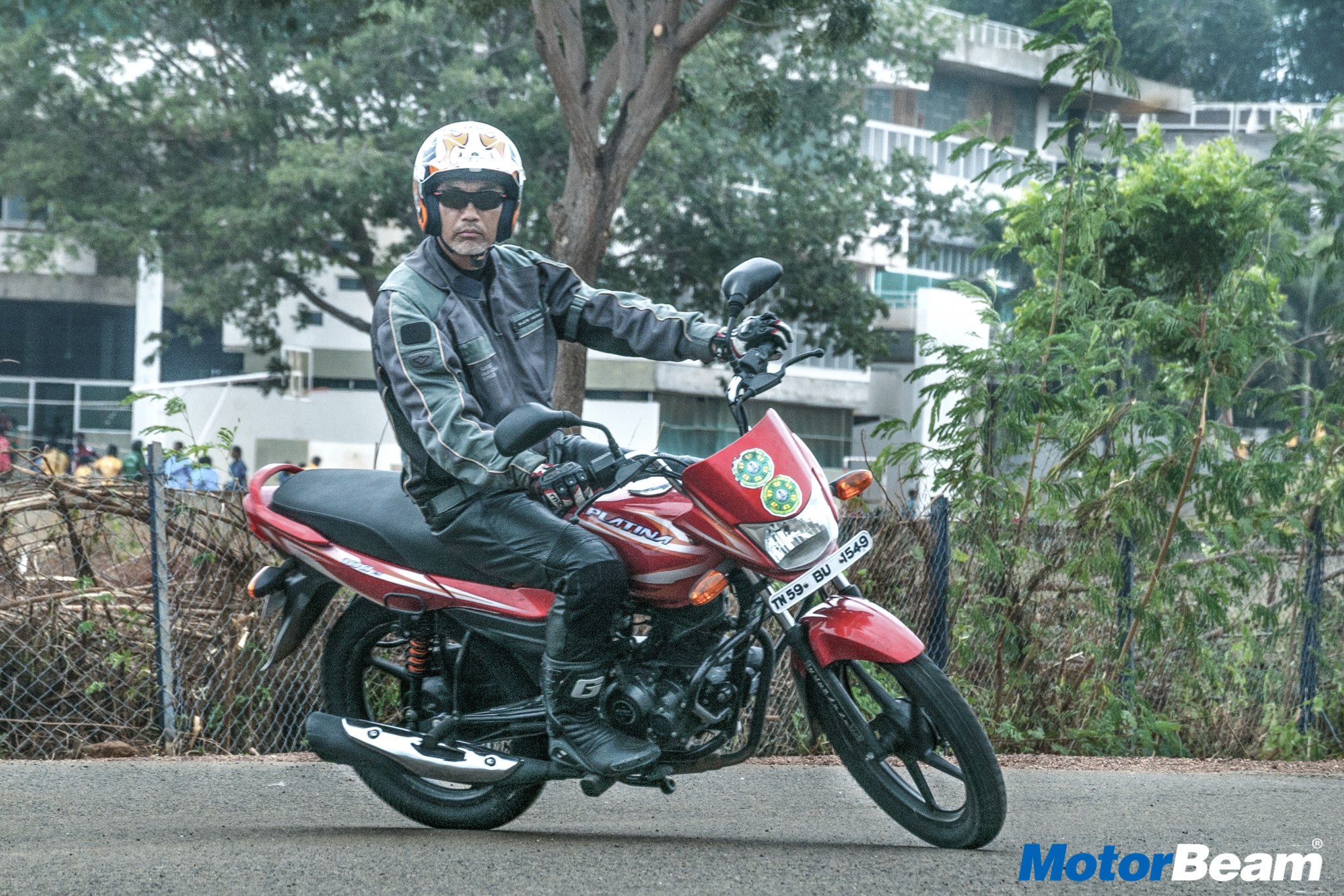
We had a lot to learn from Mr. Hide but sadly we were short of time. It seemed as if we spent most of our time at the factory or the conference room and were hardly left with any time for actual tyre testing. We were given 4 vehicles to test with different tyres on each of them. The vehicles and tyres were a Honda Activa 4G fitted with Conta 350 M, a KTM Duke 390 fitted with the Protorq CF (front) and CR (rear), a Honda CB Shine fitted with ATT 525M (front) and ATT 750K (rear), and a Bajaj Platina fitted with the same EuroGrip tyres as the Honda CB Shine. I would have loved to tell you more about these tyres but sadly we only spent the equivalent of a minute on each of these machines, riding around a figure eight course. I couldn’t properly assess the tyres but I learned a lot more about tyre manufacturing, assessment of tyres and characteristics of each individual vehicle. All in all spending all that time around tyres makes you realize how important tyres are and how much effort goes into making and developing them.