The Jaipur facility exclusively produces the Multix for Eicher Polaris witnessing 100 percent localisation for the vehicle with 102 suppliers located pan India.
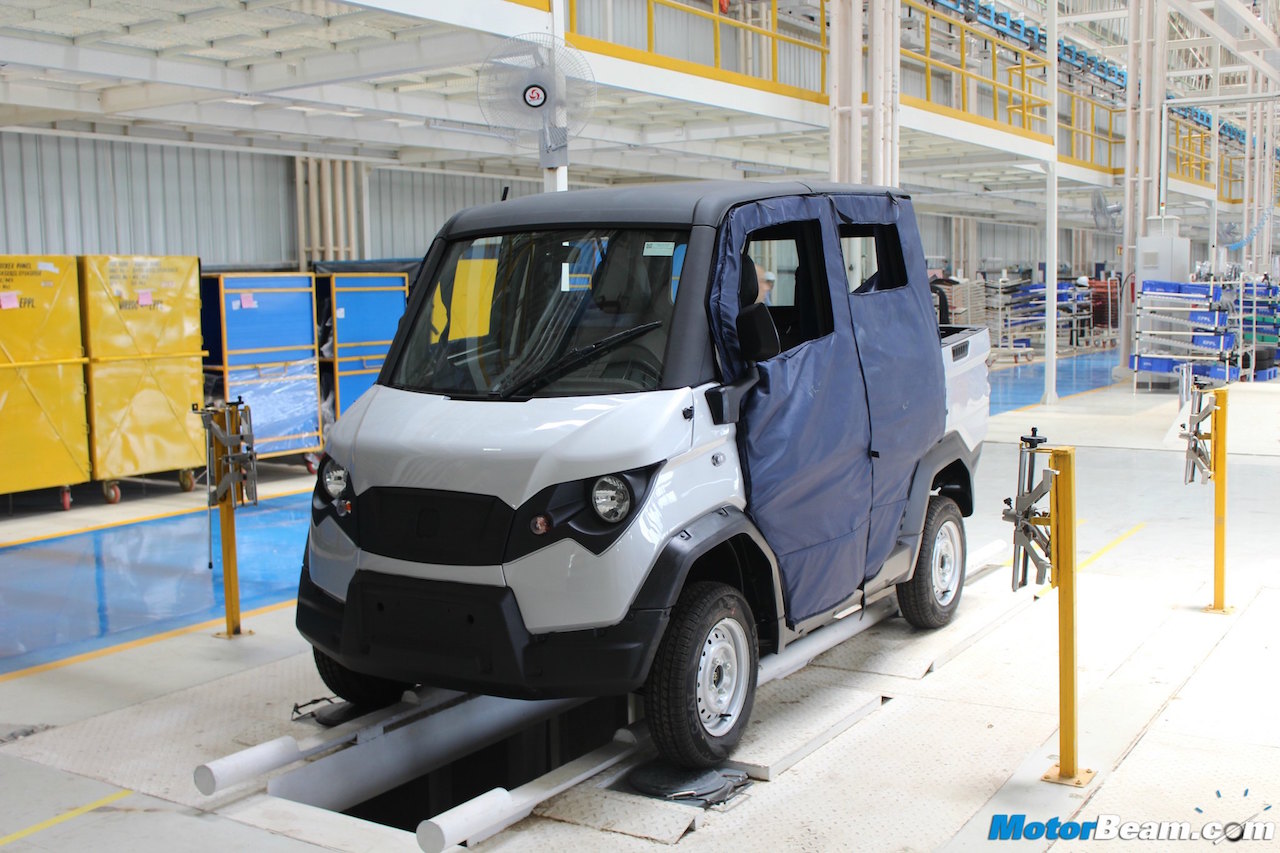
The Multix is an extremely interesting vehicle built with efficiency and optimised efforts
The intentions behind the Multix are certainly as versatile as the vehicle itself. Targeted at what Eicher Polaris calls the ‘independent businessman’, its customer base equals to a strength of 5.8 crores. The Multix comes with two rows of seating and an independent suspension system to take on rough terrain with ease but the interesting aspect are the foldable rear seats that make way for a flat-bed with a capacity of 500 kgs, all in a matter of 3 minutes. The vehicle is frugal too with power coming from a 511cc single-cylinder engine with 10 HP and an ARAI certified efficiency figure of 28.75 km/l. Then there is the X-Port unit, which converts the engine into a generator. A first-of-its-kind proposition built with a lot of thought, the Multix made us curious, so MotorBeam headed to Rajasthan for a factory tour to witness a combination of three vehicles – car, load carrier and a pickup truck, come to life.
The Multix was tested on rigs in the US with a torture track ratio of 14:1
Located in Kukas, just outside of Jaipur, the Eicher Polaris facility was established in 2013 and sits on a 25-acre property, of which the plant only occupies 6 acres, employing 180 personnel. The joint venture has made an investment of Rs. 350 crores till date towards product development and infrastructure cost at the plant that is capable of producing 60,000 units annually and can be scaled up to 1,20,000 units with an increase in shifts. The plant also takes pride in being environment-friendly and gets an innovatively designed roof to allow natural light to enter the facility, negating the use of artificial light during the day. In fact, this also helps keep the overall interior temperature 4-5 degrees lower, when compared to the scorching heat outside.
The plant tour begins with a brief on safety instructions and details about the plant
Our arrival at the Eicher Polaris facility was greeted with safety gear comprising of a helmet, face mask and a walkie-talkie in order to keep “our” moving parts in place. The Jaipur plant exclusively manufacture’s the Multix and houses a welding department, in-house paint system and assembly line. The plant also houses an R&D facility and a rigorous test track. Achieving higher economies of scale, the Multix accounts for 100 percent localisation, sourcing components from 102 suppliers spread across the country.
The weld shop fabricates around 67 units every day in a single shift
The first phase of production commences with the welding process bringing the components together to build the tubular frame. The weld shop houses 13 robots to conduct high-speed welding that are installed with anti-collision sensors to avoid accidents. Interestingly, 80 percent of the welding process is robotic, while 20 percent is manual and helps guarantee high precision welding. Stringent quality checks are performed to look for any defects, which are rectified before being sent over for the paint process. Once prepped up, the tubular frame is transported to the in-house paint shop located in the adjacent building via an overhead automated line.
The automated line takes the Multix’s tubular frame through the entire paint shop
The Multix has been thoughtfully engineered to offer a load of benefits
The paint shop is a mix of manual and automated departments wherein the tubular chassis is galvanised and powder coated to ensure anti-rusting and a longer life. Moving down on the automated line, the frame heads inside the massive powder curing oven for 40 minutes, an extremely large heat treatment unit that melts the powder coating which sticks to the body, while the overall drying process provides higher strength and durability.
The paint process and powder coating use both robotic and human input
Along with the frame, other components are also painted and stocked to be taken to the assembly line for the final process. Throughout the paint process, none of the parts are handheld in any way in order to ensure superior levels of paint and powder coating. The shop also reuses the extra powder that is collected at the end of the coating process. The plant has also optimally utilised its space, stacking up components vertically.
The painted body ready to take shape on the assembly line that is divided into 20 stations
Once the paint section is complete, the frame and other body panels head over to the 80-metre long single slat conveyor assembly line that has a team of personnels bolting parts onto the Multix. The assembly line is further divided into 20 stations starting with axles being installed first, then the suspension, brakes and steering components, and is followed by the 511cc single-cylinder diesel engine. There is also a 25-metre long assembly line with 11 stations for the gearbox assembly. The main assembly line sports a special brake fluid bleeding and filling machine as well as an automatic radiator water filling machine to make the task easier.
Axle, suspension are installed first, followed by engine, interiors, body & finally tyres
Moving forward, the interior starts taking shape as the steering rod, pedals and bench style seats are fixed on the frame. The dashboard is inserted later with the instrument cluster, integrated gearshift lever and steering wheel, thereby completing the process. Up next, body panels including the front fenders, roof, doors and windshield are mounted on the Multix, while the bonnet and tyres are one of the last components to be affixed on the multi-utility vehicle. Made out of reinforced plastic, the exterior parts would be reasonable to repair on the Multix and replacing broken panels won’t be too heavy on the pocket either. In fact, the company says that replacing a fully painted door will cost around Rs. 500/-. Talk about affordability!
The Eicher-Polaris Multix in its final stages of assembly
Eicher-Polaris has done some clever thinking when making the Multix plant
The final aspect of bringing the Multix to life includes multiple quality checks. Once the assembly is complete, the Multix heads over to the dynamometer to inspect the speedometer calibration, side slip, braking and toe in toe out testing. The versatile vehicle is then sent off for a test run to see if all parts are in working order. The test drive ensures that the Multix is in the best of health and can be shipped off to the 30 dealerships across the country. Fun Fact! During the testing phase, the development team stuffed in as many as 19 passengers (a common sight on several vehicles in rural areas) inside the Multix to see its load carrying capabilities on Indian roads.
The Multix doubles up as a generator with 3 kW of power, pumping out 1000-litres per min
Our plant tour concluded with a demonstration of the Eicher Polaris Multix’ electricity generation capabilities. With the help of an external unit called as the ‘X-Port’, the rear mounted 511cc engine can be doubled up as a generator, producing up to 3 kW of peak power. A thoughtful addition and the only passenger vehicle of its kind to offer such a facility, the X-Port unit is capable of powering an entire home or pump out water, among other possibilities.
The smaller engine offers better returns when compared to a conventional tractor
Seen here, the system is displacing 1000-litres of water per minute, which would cost around Rs. 40/- per hour and could do so for around 15-odd hours on a full tank (12-litres). In comparison, a tractor would do the same for Rs. 100/- per hour. You can also control the power output for the engine depending on the utility that further helps make the process efficient by reducing fuel consumption. With the single-cylinder engine being a liquid-cooled unit, the company says heat dissipation isn’t a problem when used as a generator.
The Multix is ready after quality checks, to be shipped out to dealers across India
The thought behind developing the Multix is quite noble and something does stick around with you longer than you would imagine. Targeted at the rural market, Eicher Polaris aims to solve the customer’s dilemma of having to choose between a car or a pickup, despite having the need for both. As the automaker describes the Multix, it is a ‘Personal Mobility Vehicle’ that will carry your family in relative comfort, but will also double up as a load carrier when needed. However, will the independent businessman be able to identify with it? That only time will tell as the Multix gears up to commence deliveries in August this year.
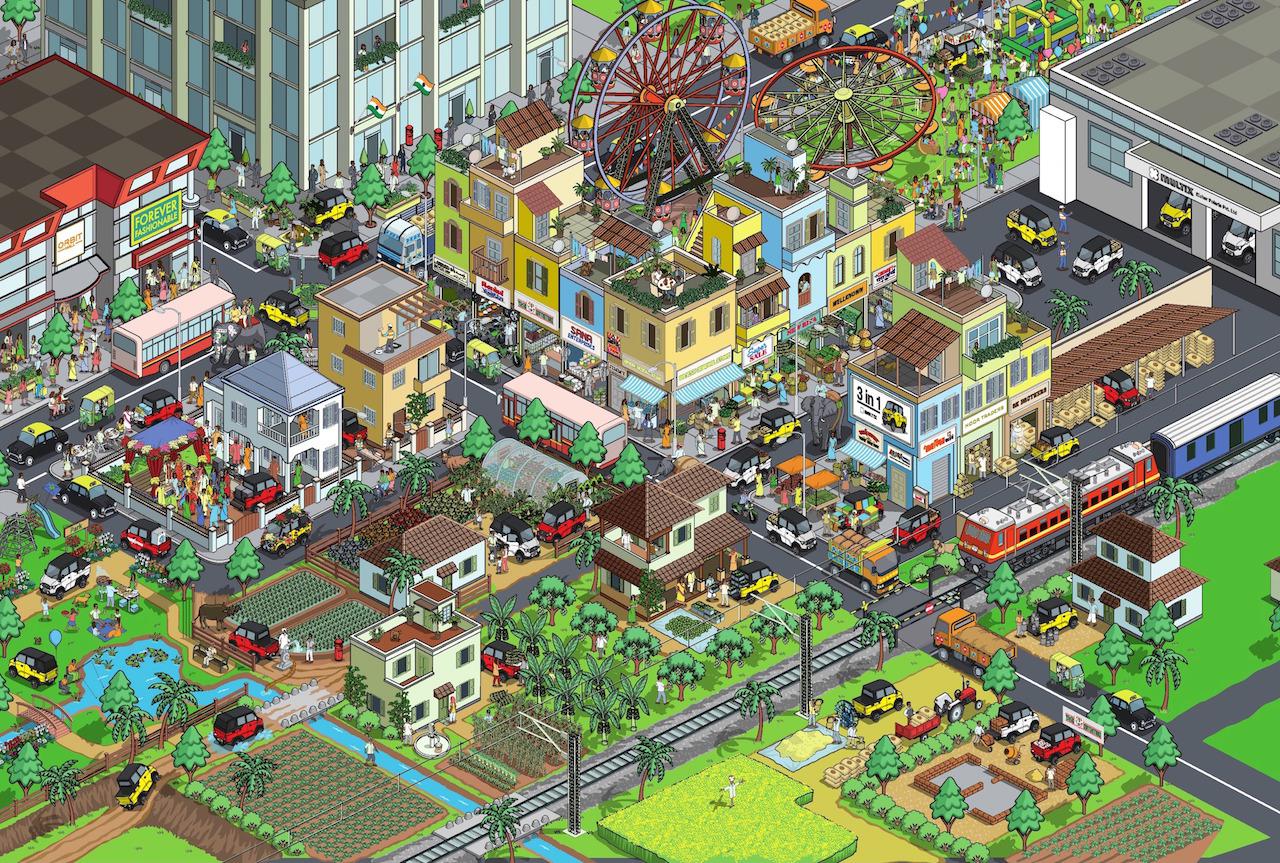
Eicher Polaris Plant Tour Key Pointers –
1) Eicher Polaris will be expanding to over 100 dealerships over the next two years.
2) The badges Eicher and Polaris won’t be seen on the Multix nor at the dealerships. The automaker wants to build the new brand independently.
3) Eicher Polaris will also be using mobile marketing in a bid to reach customers more effectively.
4) Customers will be given a personal car buying experience with the Multix and not like that of a LCV.
5) The Greaves sourced engine is a BS III unit but the company will introduce a BS IV version in the future.